Will Britain’s “right to repair” law fix anything?
A new law is designed to make it easier to mend broken tech, but experts say it doesn’t go far enough
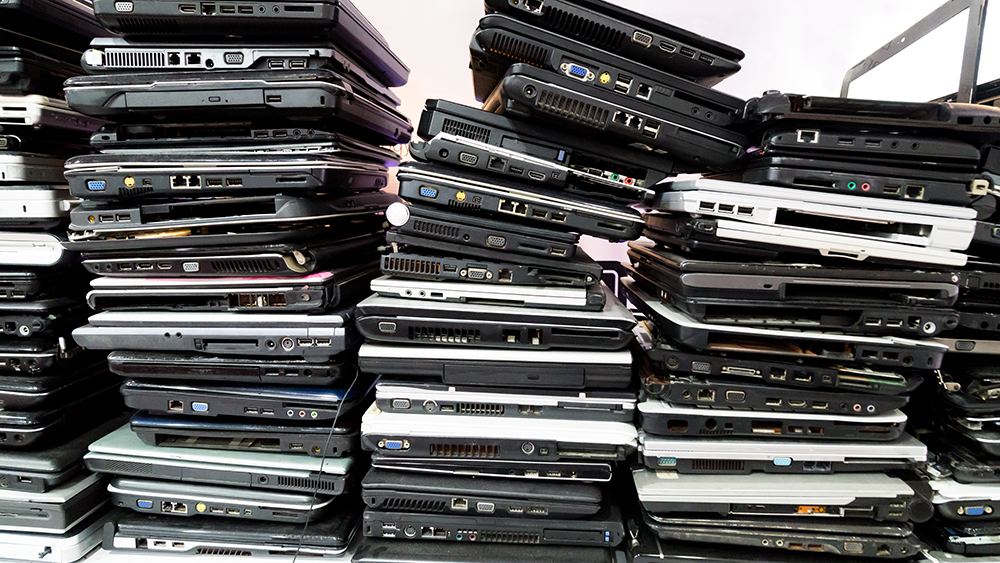
Broken laptops are piling up in recycling centres. Cracked displays are shovelled into landfill sites. Don’t even ask about the mountain of white goods that we throw away each year.
Britain generates 1.45 million tons of electrical waste every year, according to Material Focus, so it’s perhaps just as well that a new law has come into force designed to encourage us to repair broken tech and not just throw it onto the scrapheap.
“Under the new law, manufacturers of certain categories of products will have to make spare parts and repair information available for at least seven to ten years after a product is retired from the market,” says Ugo Vallauri, co-founder of the Restart Project, a London-based social enterprise that campaigns against what it calls the “throwaway, consumerist model of electronics”. Instead, it advocates that consumers should have a “right to repair” the gadgets they buy to reduce e-waste.
So, is the law fit for purpose or a pile of rubbish? The answer is analogous to fixing your iPhone: complicated.
Gaps in the law
“Everyone should have the right to decide whether a product they own should be repaired and by whom, including making sure that we can decide to repair it ourselves,” Vallauri adds, describing the three core demands of the right to repair movement as: having access to tools and spare parts; having all of the information accessible, including things such as schematics and instruction manuals; and having the repair be affordable.
“For the first time ever, in so-called ecodesign regulations, the repairability of products is factored in and that is a really important step because it will help change the design of future products to make them more repairable."
Although iPhones are notorious for being difficult to repair, Apple has recently launched a self-repair scheme
Sign up today and you will receive a free copy of our Future Focus 2025 report - the leading guidance on AI, cybersecurity and other IT challenges as per 700+ senior executives
Alas, in his view, the new law also falls short in several ways. “It’s far from being an actual legal right to repair,” he continues, “It doesn’t apply to products that we already own. It only applies to new products that are put on the market. So, it’s not as if manufacturers are under any obligation to make spare parts for existing products that people already have.”
Another problem Vallauri identifies is that the majority of parts listed in the legislation are only to be made available to professional repairers. Consumers are mostly only granted a right to purchase new consumables, such as spare plastic cutlery trays for dishwashers, rather than anything that might require a screwdriver or a soldering iron to install.
He also worries that the new law is silent on the affordability of spare parts. “A manufacturer could be complying with the legislation without making any part available whatsoever at a price point that doesn’t push people to replace a product,” he says. “The legislation is really not going far enough.”
There’s one other glaring problem: at the moment, the law only covers a meagre selection of products, such as washing machines, dishwashers and large screens. “This is for white goods, and it doesn’t take into consideration the repairability of laptops, tablets and smartphones,” Vallauri says.
In response, he's launched a petition urging the government to be more ambitious and expand the law to cover our computers and phones.
Refurb blockers
Nick Glynne is the founder and managing director of the Buy It Direct Group, which, in 2018, acquired reverse logistics firm Trojan Electronics. Each year, the 150 people in Trojan’s engineering team refurbish and repair 150,000 items. In principle, he’s very sympathetic to the concerns that motivate the right to repair movement.
RELATED RESOURCE
IT Pro 20/20: Using technology to create a better future
Issue 21 of IT Pro 20/20 looks at the newest innovations and projects shaping our interactions with the world around us
“I just think it’s totally outrageous really,” he says of the current situation. “If you bought a BMW, you’re not going to sign a contract that says in five years’ time you won’t be able to get any spare parts for this car and that’s it, if it breaks your finished, you’ve got to throw it away.”
He’s also concerned about e-waste, pointing to the behaviour of a well-known vacuum cleaner manufacturer he worked with as a shocking example. “That company wanted to protect its brand and its experience to such a degree that it refuses to allow any of its products to be refurbished,” he says. “All returned products, for any reason, were crushed and sent to landfill.”
iPhones are also frustrating for refurbishers. As they are locked to particular users, even after being reset, the iPhones he receives are often only good for parts.
Unintended harms
Glynne's also sceptical of some aspects of the new law and worries there could be unintended consequences. “We buy white goods ourselves so now we’re responsible to make sure those parts are available in the market for ten years, and it’s really hard to do that,” he says, explaining that Chinese manufacturers work on “spot buying”, where components are bought from their suppliers in one go, at one point in time. This means there’s no steady supply chain to go back to for spare parts after the batch of devices have already been made.
The law only covers a narrow
One option is to buy up plenty of spare parts at the time devices are manufactured, but this also isn’t particularly viable. “How the hell are you going to judge which spares you buy in at the time, that are going to last ten years? For small importers like ourselves, it’s really challenging. You’re either going to end up with a whole lot of excess spares sitting there, or you’re going to get sued by someone for not having enough spares in,” he continues.
“We throw out hundreds and hundreds of spares every year because we’re cautious, we bring in spares to protect the product,” says Glynne. “What happens in ten years’ time when your obligation stops? What are you going to do with all those spares?
“All that carbon cost in manufacturing them. All that cost and shelving them and storing them. And then what are you going to do with them when you get rid of them? That’s an unseen consequence of the law.”
He also points to the reverse logistics involved in repairing and refurbishing, and the added carbon impact of transporting irregular items and parts to where they may need to be. “The chances of a refurbished product breaking in the first three months is three times higher than a new product,” Glynne says. “It may be because [customers] don’t understand what refurbed is, it may be because it’s too noisy. It’s maybe because it’s a little more scratched than they thought. Whatever it is, it’s rejected and the whole cycle starts again.”
The impact of British law alone is likely to have limited impact on the behaviour of manufacturers. Unlike the US, China and EU, the UK isn’t a regulatory superpower. But Vallauri does believe there's one area where the law could be tightened, by more tightly regulating after-sales service. He suggested, for example, that we could remove VAT on repair services, or we could follow France’s lead in scoring products on their repairability (as with nutritional labels on food) to provide consumers with more information on what they are buying.
“The UK could actually have a big impact,” he says.
-
Developers aren’t quite ready to place their trust in AI
News AI coding tools are delivering benefits for developers, but they’re still worried about security and compliance
-
Are chief AI officers here to stay?
In-depth Mainstay of the boardroom or short-term project leader, CAIOs are the subject of intense consideration