easyJet trials drone safety checks, VR training and 3D printing
Budget airline easyJet will use drones to check aircraft after lightning strikes
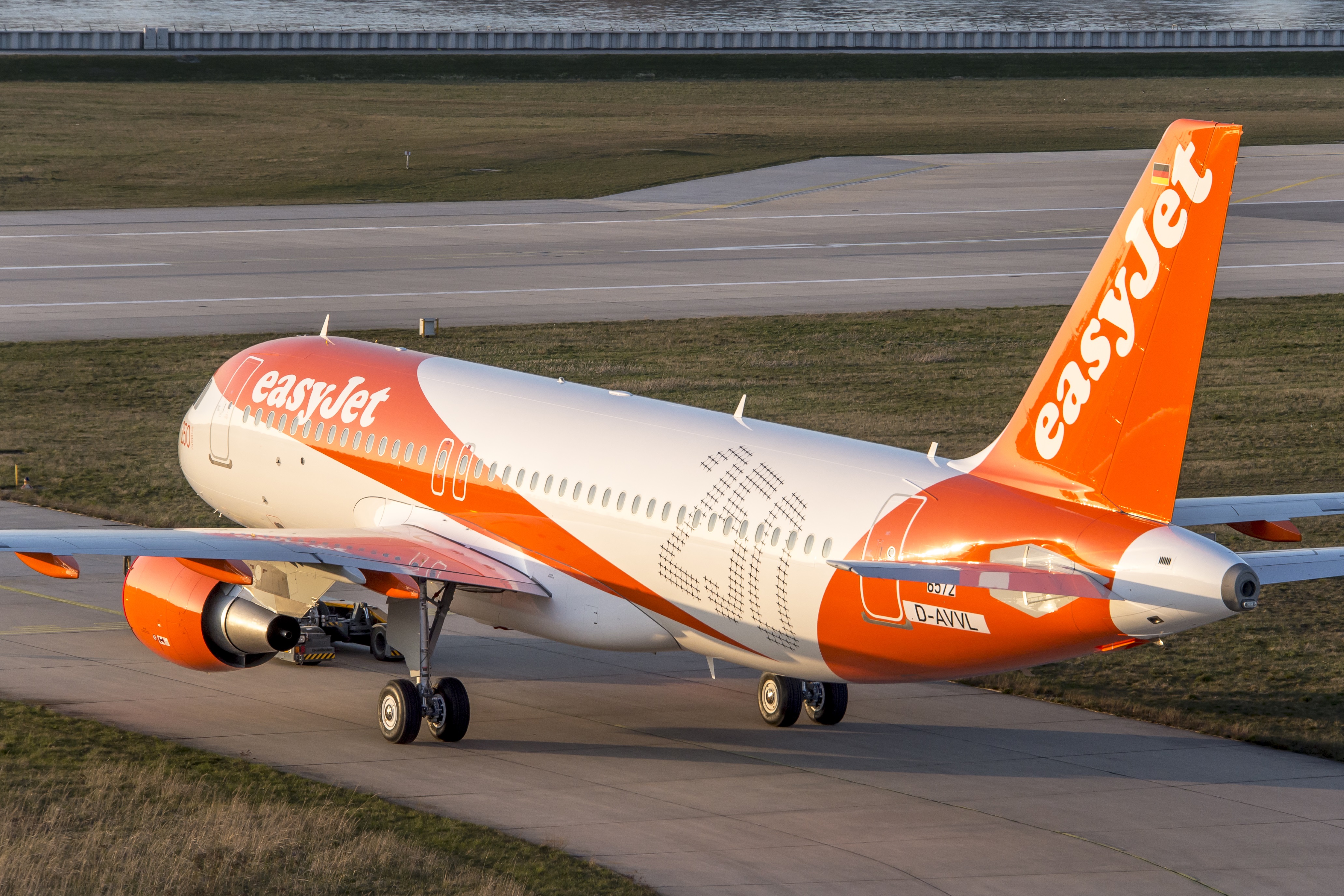
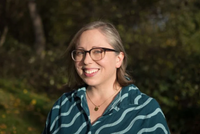
Drones will help run safety checks for easyJet aircraft starting next year, the budget airline announced, saying it was also trialling 3D printing to make replacement parts.
Automated, preprogrammed drones will look over aircraft that are out of service because of events such as lightning or bird strikes, easyJet said, helping to bring them back into service more quickly than with manual inspections alone. The airline believes it will cut the time planes are out of use from days to hours.
The drones have already been successfully trialled on one aircraft, and easyJet is convinced the drones will help it cut costs enough that it will deploy them to up to ten engineering bases within the next year, including London Luton and London Gatwick.
Made by Blue Bear and Createc, the drone system is also used for maintenance on ships and buildings.
The airline has other high-tech ideas to cut costs, and said it will trial using 3D printers to create replacement parts for arm rests and other in-cabin items, hoping to cut back on storing spares and stop waiting for replacements.
3D printed replacement engine parts are also on the horizon. The next engines easyJet will use are called LEAP, and feature 3D printed fuel nozzles, carbon filter fan blades and more.
The new technologies don't mean easyJet will be skimping on maintenance or safety staff, the company stressed. "The use of these emerging technologies frees up our engineering and digital teams to enable them to undertake more skilled tasks, keeping our costs down which in turn keeps our fares low, helps minimise delays and ensures that we maintain our industry leading punctuality for our passengers," said head of engineering Ian Davies. "Safety is our number one priority and so all of these new technologies will be applied by our experienced engineering and flight crew to ensure our leading safety record is maintained."
Sign up today and you will receive a free copy of our Future Focus 2025 report - the leading guidance on AI, cybersecurity and other IT challenges as per 700+ senior executives
Software and apps
Alongside the new hardware, easyJet is working with a trio of firms to test the use of virtual reality for staff training. One idea is to use 3D laser scanning to create a digital model of a plane's cabin so that staff can learn where everything is located. Another idea is to use gaming technology to simulate customer service scenarios.
easyJet is also working with Airbus on new diagnostics software to spot problems before they cause technical delays, and is working on new apps for the iPhone and Apple Watch.
CEO Carolyn McCall said easyJet has been steadily shifting to new technologies over the past year, moving to paperless cockpits, and developing apps to help track maintenance issues such as fan changes after a bird strike.
"Since then we have continued to look for new and original innovations to help run our operation smoothly and ensure passengers get to where they need to go safely and on time," she said.
"All of this work is aimed at further increasing reliability of our aircraft and therefore improving our passengers' experience," she added.
Freelance journalist Nicole Kobie first started writing for ITPro in 2007, with bylines in New Scientist, Wired, PC Pro and many more.
Nicole the author of a book about the history of technology, The Long History of the Future.
-
Is the traditional MSP service desk dead?
Industry Insights AI and B2C expectations are reshaping B2B service desks and MSP strategy
-
From phone calls to roll calls: 3CX has the answer
How Yellowgrid, a 3CX Platinum distributor, has taken advantage of 3CX Phone System’s customisable nature to create a time-saving solution already embraced by over 100 UK schools