How Trek used mobile device management to optimize its wearables fleet
The cycling giant rolled out mobile management tools to keep its warehouse devices secure and cut service times significantly
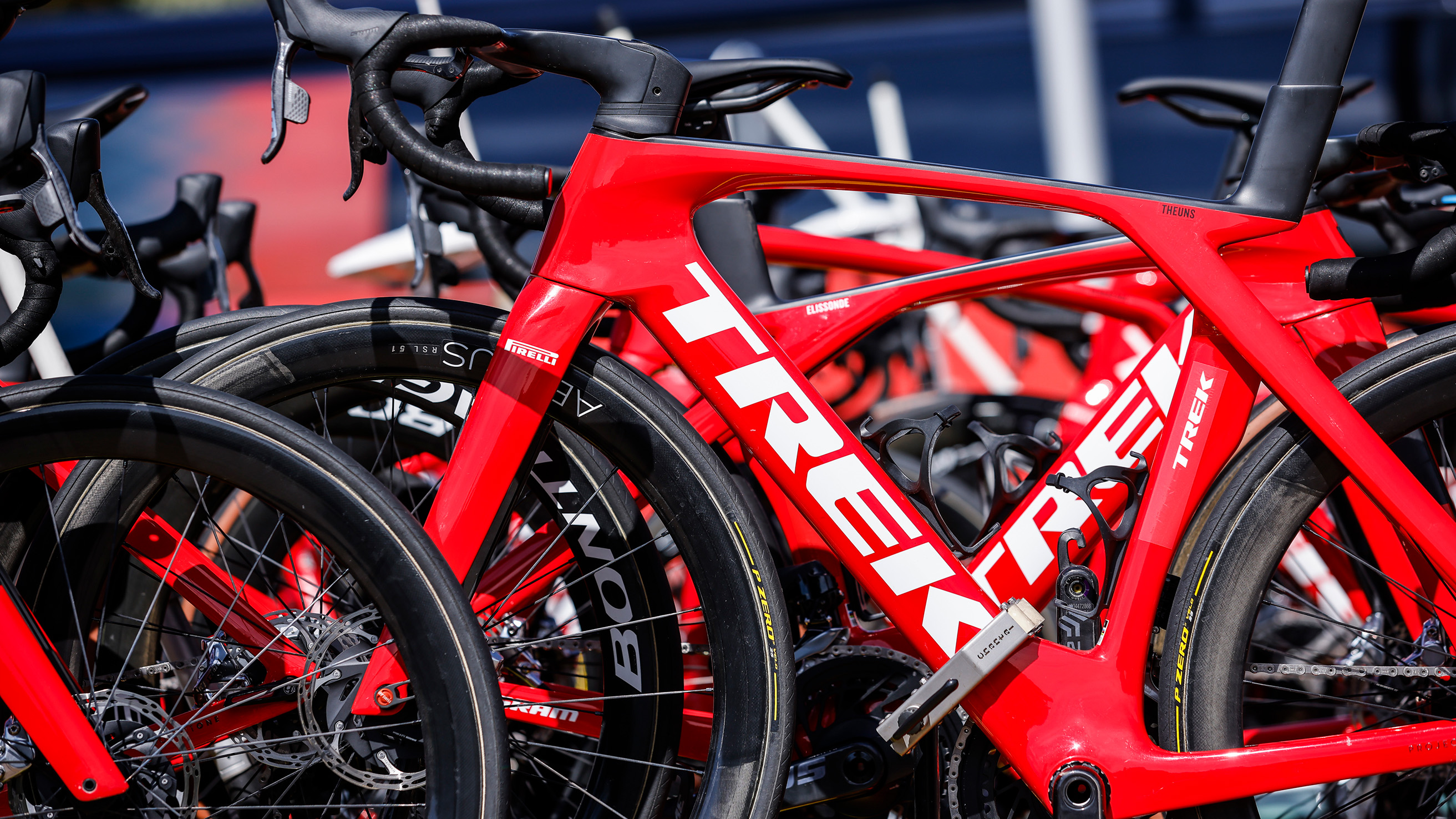
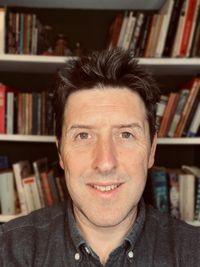
Bicycle company Trek has implemented a set of enterprise mobility management tools that have helped it track and secure its fleet of hundreds of wearable devices to boost efficiency and availability.
Trek has been a leading bicycle retailer for over 45 years, with operations in 80 countries around the world. It has warehouses in the US and Europe where hundreds of staff use wearable devices to help them pick and keep track of stock. However, the company struggled with device downtime due to a lack of visibility into the status and health of its wearable hardware.
Tom Spoke, director of global IT at Trek Bicycle Corporation, tells ITPro that the firm has three large warehouses in North America, in addition to three in Europe and two manufacturing facilities. Across those eight locations, staff use handheld devices or wearable scanners to go about their daily tasks. This includes collecting data, receiving inventory, and inventory management like replenishing pick locations from overstock as they empty. The devices are an integral part of Trek’s general picking and shipping process.
Trek uses Android-based devices, with staff using a wearable on their wrist and a Bluetooth fingertip scanner. Spoke notes that staff need to be hands-free because they need to use both hands to pick stock, hence why wearables work so well.
“There’s a lot of different activities that our warehouse and our manufacturing staff are doing on their wearable devices and for many years we’ve had a challenge managing those devices and the software that runs on them,” Spoke says.
In the past, for example, the IT team might have received a call from warehouse staff who were experiencing problems with a scanner. Trek would try to position IT staff close to these locations to go into the warehouse or the manufacturing facility and remedy these frontline issues for staff as and when they arose.
That proved a challenge because while IT staff were local to some of these facilities, others had no one in the immediate vicinity. This often led to IT workers being forced to fix problems over the phone – a process Spoke describes as “painful, absolutely painful”, adding that overall these attempts simply don’t work.
Sign up today and you will receive a free copy of our Future Focus 2025 report - the leading guidance on AI, cybersecurity and other IT challenges as per 700+ senior executives
As Trek moved to adopt more modern mobile devices throughout its warehouses, it sought a mobile device management (MDM) tool to give it a better idea of what devices were in operation and provide live device details such as battery level and Wi-Fi signal. This would allow the firm to push security updates to all of the devices and troubleshoot problems more effectively.
After evaluating enterprise mobility management tools, Trek opted for SOTI MobiControl and SOTI XSight – the aim being to ease wearable device use in its warehouses and reduce downtime.
Using SOTI MobiControl, Trek has been able to gain visibility and control over its mobile devices, with access to data on what individual devices are doing, how they’re performing, and what security risks they’re facing. Trek has also adopted SOTI XSight, which allows remote support to diagnose and fix device issues without the IT team needing to be physically present and also lets remote staff help users to fix problems themselves.
With improved device visibility in place, Trek has cut time spent on device support and updates from hours to minutes. Trek’s IT staff now have a dashboard so they can drill down and see devices and useful data analytics such as battery health, firmware version, and patching status.
RELATED RESOURCE
Spoke said that from the dashboard, staff can see a holistic picture of device health and pick up on issues such as devices that haven’t been used or are powered off. “It’s a proactive way of getting ahead of issues they might contact us for,” he tells ITPro.
“It pretty much gives them everything – they can click a button and remote desktop into the device, so that when warehouse staff are at a picking location and they’re having a problem with their scanner we can plug right into it and see what they see and take control of it,” Spoke says. “We now have hundreds of these devices across all these facilities and it’s working great.”
The devices also now come pre-configured with required software and settings, allowing warehouse staff to use scanners right out of the box.
Spoke says the shift has saved a lot of time in day-to-day support, adding that it’s also been “a huge win for our security team because now we are more effectively able to stay up to speed on our continual patching efforts”.
In all, Trek has measured a 15-20% time saving on new employee onboarding as a result of the adoption.
His advice for companies looking at the same sort of project is to “start small”. Trek took that approach, by rolling out a small number of the devices as its new German warehouse was still being set up. Once the company was happy with the progress it had made, it started buying new devices for its other warehouses and phasing out the old hardware.
“It was a pain point: it was something that we felt like it was easy for us to address, so we did it. Now that this is no longer a problem it allows us to focus on some of those other value-add projects,” Spoke says. “There is definitely a saving: our warehouse staff are happier, our IT staff supporting them is happier,” he adds.
Steve Ranger is an award-winning reporter and editor who writes about technology and business. Previously he was the editorial director at ZDNET and the editor of silicon.com.
-
Using DeepSeek at work is like ‘printing out and handing over your confidential information’
News Thinking of using DeepSeek at work? Think again. Cybersecurity experts have warned you're putting your enterprise at huge risk.
-
Can cyber group takedowns last?
ITPro Podcast Threat groups can recover from website takeovers or rebrand for new activity – but each successful sting provides researchers with valuable data