Seeing double: The rise of the digital twin
Industrial giants are pioneering the use of this technology to optimise maintenance, improve operations and generate cost savings
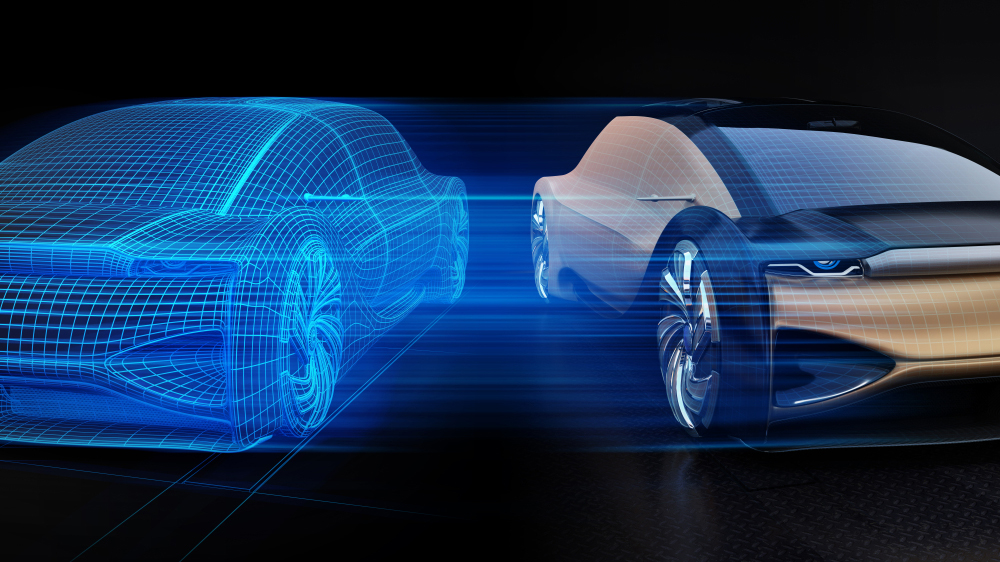
Defined by Gartner as 'a virtual representation of a thing, person or process to meet business objectives', digital twins replicate all of the features of a physical model, enabling the remote simulation, monitoring and maintenance of anything from a piece of equipment to an entire city.
US aerospace organisation NASA was one of the first to embrace digital twins. In fact, it used an early iteration pairing technology in the first days of space exploration. It has never looked back; today it is investing in digital twins to help it predict, detect and solve problems for hardware and systems located far from Earth.
Managing assets
This ability to virtually manage hard-to-reach assets is changing the game for those pioneering businesses that choose to follow NASA's example. British-Dutch oil and gas firm Shell, for example, is using digital twin technology to help it perform real-time structural integrity checks on several of its fixed and floating offshore assets.
It's a similar story for American multinational energy corporation Chevron, which is using the technology across its control process systems, such as refineries, as well as for its subsurface reservoirs. "Obviously, we can't see beneath the surface, so the digital models allow us to test different production techniques to optimise our approach when we go live," Ed Moore, Chevron's senior technology strategist for emerging technology, tells IT Pro.
The benefits don't end there. By powering a digital twin with internet of things (IoT) data, as well as artificial intelligence (AI) and machine learning (ML), firms are able to predict faults and prevent machine failure, reducing the downtime of equipment which could lead to lost production and higher maintenance costs.
Global industrial firm GE is doing exactly this. It has created digital twins of its entire jet engine fleet to better predict when engines need to come in for service. This helps its airline customers avoid losing tens of millions of dollars in maintenance costs and prevents passengers from experiencing delays.
Logistics firm DHL, meanwhile, is joining forces with food packaging manufacturer TetraPak to develop a digital twin of an entire warehouse, replicating all activities and machinery. By analysing the movement of packages and functionality of machinery, the firms expect the digital twin to dramatically improve productivity.
Sign up today and you will receive a free copy of our Future Focus 2025 report - the leading guidance on AI, cybersecurity and other IT challenges as per 700+ senior executives
Having real-time access to the condition of an asset also enhances safety if there is an issue, then a company doesn't have to wait for it to be flagged by routine inspection. "We have immediate notification of anomalous data so we can take the appropriate actions," says Chevron's Moore.
Saving time and money
Generating new efficiencies in these ways can also boost the bottom line. GE has already realised more than$1.5 billion in cost savings through predictive maintenance and enabling more optimal performance of assets and systems for its businesses and their customers.
At the same time, Italian car manufacturer Maserati has reportedly used digital twin technologies to conduct a number of virtual test drives and wind tunnel tests, reducing the number of physical prototypes it makes. This has cut vehicle development time by 30%.
It's clear that the emergence of digital twins is transforming how we build, move and power the world and experts agree that this will proliferate in the years to come.
"While our research has found that only 13% of enterprises have already implemented digital twins, another 62% are in-process or planning to implement them by next year," Alfonso Velosa, vice president of research at Gartner, explains to IT Pro.
NASA will continue to spearhead the use of the technology. In fact, its Aeronautics Research Mission Directorate (ARMD) division has recently developed elements of the digital twin in a project that, when matured, promises to revolutionise certification, fleet management and sustainment of vehicles and applications.
"Digital twins could be a key enabler for NASA to bring about substantial improvements in affordability, performance and capabilities," John Vickers, NASA principal technologist in the area of advanced manufacturing, tells IT Pro. "It's likely that NASA's use of digital twins will only increase."
Paving the way for success
While the future undoubtedly looks promising, it will take the widespread adoption of key enabling technologies such as IoT, AI, ML and augmented reality (AR) for digital twins to enter mainstream use.
"IoT is needed to collect data from the physical world, cloud-based IT systems are required for storage and processing, machine learning will help enable prediction, and ideally some form of virtual, mixed, or augmented reality should be used to help consume the information from the digital twin in a more immersive way," says Ben Gesing, senior innovation manager at DHL Customer Solutions and Innovation. "These technologies will lay the groundwork for digital twins."
When this eventually happens, the possibilities will be endless.
In the years ahead, GE expects its digital twins to augment its industrial machines, services and manufacturing processes with more intelligent capabilities to not only generate, distribute and consume energy in cleaner, more sustainable ways, but to optimise air travel to increase the number of passengers served with minimal or no disruptions.
And Chevron will go a step further. "Using Microsoft's AR solution HoloLens, we're already able to create 3D true-to-scale holograms of designs of ships or refinery units, which are overlaid in a physical environment," says Moore. "In the future, we anticipate having full 3D virtual representations of our end-to-end operations, from the truck driving through the gate, to product delivery at the other end."
-
These are the UK industries facing the biggest digital skills gaps in 2025
News Analysis of job vacancies shows that the digital economy is accelerating too quickly for the workforce to keep up with
-
Telefónica Tech UK&I names Martyn Bullerwell as new CEO
News The company veteran succeeds Mark Gorton who steps down following three years in the role
-
Achieving business outcomes with generative AI
Webinar Take your hybrid cloud journey to the next level with generative AI
-
The three keys to successful AI and ML outcomes
Whitepaper Unlocking the potential of machine learning in the generative AI era
-
Clarity of AI implementation is a primary concern for UK employees
New research finds workers are enthusiastic about implementing AI but are in the dark over how it will happen
-
Operational efficiency and customer experience: Insights and intelligence for your IT strategy
Whitepaper Insights from IT leaders on processes and technology, with a focus on customer experience, operational efficiency, and digital transformation
-
The four pillars of excellence for technology leaders
whitepaper Download this CIOs business case for integration and automation
-
Sustainability at scale, accelerated by data
Whitepaper A methodical approach to ESG data management and reporting helps GPT blaze a trail in sustainability
-
Bing and Edge AI hits open preview, with chat history and multimodal promise
News Bing and Edge have been given a visual boost, and will now support third-party integration
-
How to help IT manage itself with autonomous operations
Whitepaper Using AI and automation to proactively adapt to business disruptions