IT in manufacturing isn’t just about the production line
From conception to execution, IT is used in manufacturing to boost efficiency, reduce costs, and produce optimal results
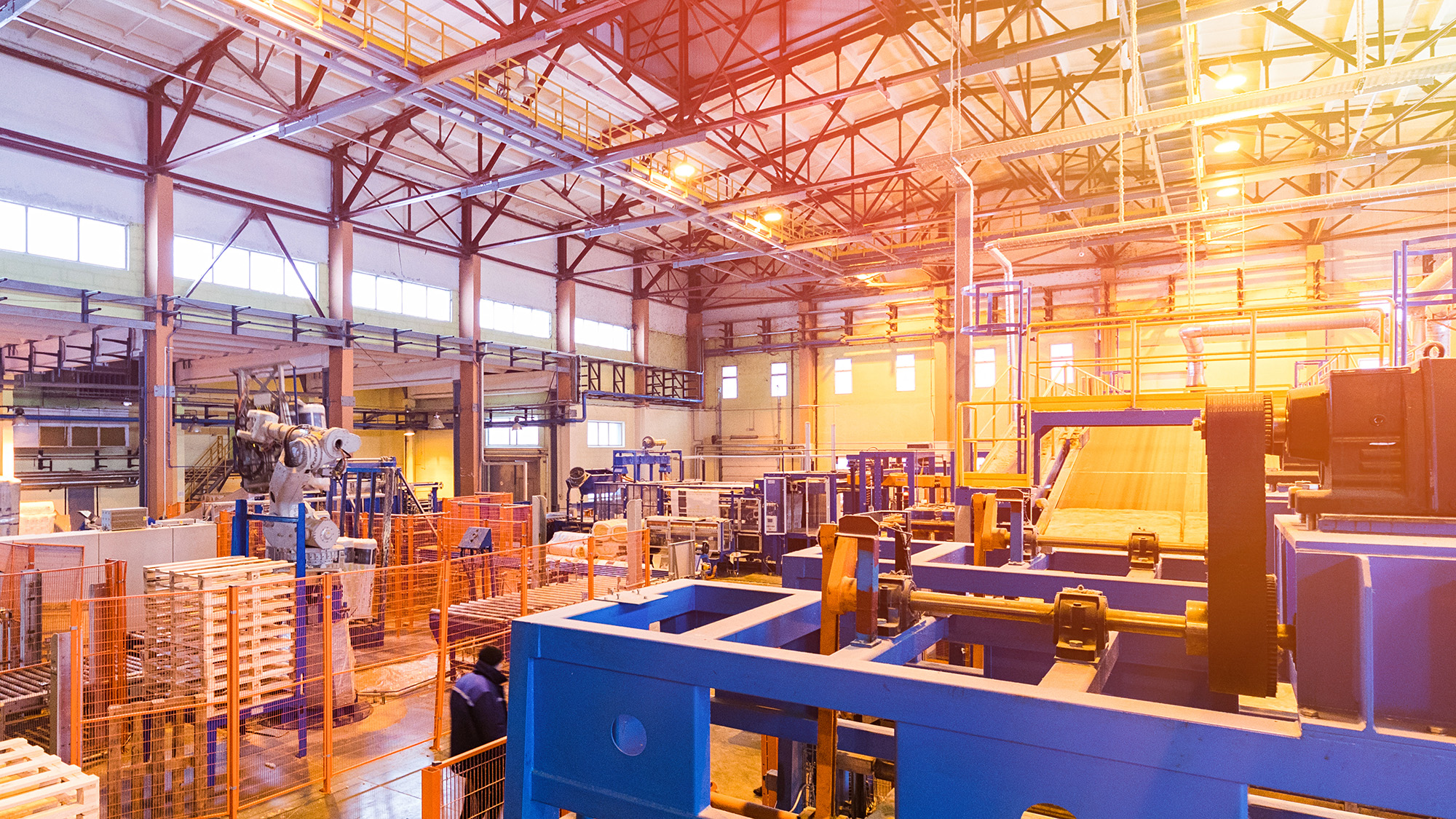
In the 21st century, the worlds of IT and manufacturing are indivisible. Digital solutions shore up manufacturing processes inside and outside the factory line, helping to improve efficiency and empowering workers to do more than they ever could before.
While attention is often given to the digital revolution happening on factory floors, there’s a whole industry of IT work that goes into the manufacturing space before tools are raised. For every robot arm on the production liner, there is a server stack or 3D file that has been put together by IT and computer design teams as a bridge from initial ideas to the physical world.
Computer-aided design (CAD) software helps designers, architects, engineers, and those in similar professions to render 3D designs in extreme detail. This could be for drafting or proposal purposes, but it can also be used as a precursor or feed directly into the manufacturing process when it comes to waterjet cutting or additive manufacturing (often called 3D printing).
CAD software can also be incredibly resource-intensive, however, so businesses looking to use it with any regularity need to invest in competitive hardware. This is because it has to manage thousands of points of data within each render – each curve, point, or facet of a 3D shape is stored by workstations as a complex mix of mathematical equations. These are translated into visual files through a process known as vector graphic rendering, before being used as the blueprints for precision architecture, manufacturing, and engineering.
This resource intensity has been compounded in recent years with the introduction of ray tracing into many popular CAD software suites. Ray tracing uses an algorithm to realistically simulate light within a 3D environment. Beyond helping renders to look far nicer, ray tracing also allows engineers to produce projections for the transfer of heat across a specific render, or how it interacts with ambient versus direct lighting.
These are important considerations in areas such as renewable energy, or for planning devices intended to be used in a range of challenging environments such as vehicles or light-sensitive equipment.
Silicon as a necessary investment
Businesses must choose wisely when it comes to investing in IT throughout their supply chains. It’s not much use to pour money into smart manufacturing without backing your data centers with the chips necessary to keep all your workloads running smoothly.
Sign up today and you will receive a free copy of our Future Focus 2025 report - the leading guidance on AI, cybersecurity and other IT challenges as per 700+ senior executives
RELATED WHITEPAPER
Taiwan Semiconductor Manufacturing Company (TSMC) uses AMD’s EPYC processor family heavily for its IT backend, as a core piece of hardware throughout its data center environment. When TSMC moved to a hyper-converged infrastructure (HCI) configuration for its servers, it found EPYC central processing units (CPUs) to be highly capable and compatible with its existing virtual machine setup.
The semiconductor giant uses silicon at the front of its productions too, having deployed some of the latest EPYC CPUs within its manufacturing environments to run all the complex automated machines within a semiconductor factory. Ultimately this comes back to the degree to which hardware has been integrated into the company’s server architecture, as the physical elements of automation throughout its factories rely on around a thousand virtual machines. These are run on server stacks containing EPYC CPUs, which support the kind of vast memory needed for the scale of the workloads without sacrificing throughput or cost due to its 128-lane, single-socket design.
With dedicated workstations, IT teams can also combine powerful CPUs with graphics processing units (GPUs) to distribute the intensity of workloads across the hardware best suited to the task. Processor power is the major demand from CAD software, alongside hefty RAM, but for the most graphically-intensive tasks, it’s important to have a strong GPU in place in case tasks need to be split across multiple cards for more efficient processing.
In the future, generative AI may allow design teams to quickly create production models using only text input via natural language processing. This will compound the need for powerful GPUs within workstations.
Measure twice, cut once
Graphics cards and processors can also be used to perform data analytics or run advanced simulations. This allows design teams to quickly cycle through iterations of a design to ensure no time is wasted producing sub-optimal components when it comes to the manufacturing stage.
In this way, businesses can cut costs that would have been spent on manufacturing physical proofs-of-concept for products while also saving hours, days, and weeks spent stress-testing products to determine if they have been built to the best standard. For example, Orca3D LLC used AMD Threadripper CPU technology for its Orca3D marine design software to draft hull shapes, stability, and geometry to help manufacturers in the maritime industry produce seaworthy vessels.
This was combined with a package from the company Simerics, used to add computational fluid dynamics to Orca3D to assess the buoyancy and water resistance of designs and how individual control surfaces across a vessel fare in a dynamic ocean environment. All of these elements combined make for an intensive computational challenge.
Simulations can be especially important for emerging fields such as clean technology or products that use novel materials with unknown properties and high costs. Running virtual tests with cutting-edge hardware allows manufacturers to pull any anomalous behavior to the surface that could cause problems down the line, while also giving them concrete data on the various benefits of new materials.
It’s worth noting that simulation also has an important role to play in more familiar territory such as the automotive industry, where manufacturers run simulations to assess the safety and efficiency impacts of the most granular design changes. AMD says its EPYC processors can help manufacturers scrutinize crash tests or drop tests at up to 1.99 times the max performance per core versus Intel’s Xeon CPUs and analyze product structures 1.33 times faster too.
At the highest levels of processing power, enterprises can create digital twins to simulate entire environments and probe changes to unlock efficiency gains or reduce costs. This is an example not only of IT feeding into the manufacturing process but also of how it can improve entire manufacturing floors. For example, a business could use a digital twin to simulate the movements of autonomous robot arms on a conveyor belt, or discover a better design for a production line that boosts manufacturing output.
Whether it’s in the data center or a workstation, CPU and GPU performance is as important in manufacturing technology as anything found on the factory floor. Knowing what hardware to employ is a key part of running a successful operation.
ITPro is a global business technology website providing the latest news, analysis, and business insight for IT decision-makers. Whether it's cyber security, cloud computing, IT infrastructure, or business strategy, we aim to equip leaders with the data they need to make informed IT investments.
For regular updates delivered to your inbox and social feeds, be sure to sign up to our daily newsletter and follow on us LinkedIn and Twitter.
-
Using DeepSeek at work is like ‘printing out and handing over your confidential information’
News Thinking of using DeepSeek at work? Think again. Cybersecurity experts have warned you're putting your enterprise at huge risk.
-
Can cyber group takedowns last?
ITPro Podcast Threat groups can recover from website takeovers or rebrand for new activity – but each successful sting provides researchers with valuable data
-
AMD names new VAR and SI commercial sales chief for EMEA
News James Blackman is tasked with building a robust channel community in the region
-
AMD to cut around 1,000 staff to focus on "growth opportunities"
News The AMD layoffs come after rival Intel cut staff on the back of flagging AI returns
-
Everything you need to know about AMD
In-depth A quick guide to AMD, one of the world's leading semiconductor companies and a longstanding competitor to Intel and Nvidia
-
Optiver partners with AMD to turbo charge data center modernization efforts
Supported Content AMD will support the market trading firm as it looks to deliver performance improvements and meet future data needs
-
AMD bags IEEE’s 2024 Corporate Innovation Award for pioneering chiplet design research
Supported Content This marks the second time AMD has received this award, having previously been recognized for its research into the evolution of x86 microprocessors
-
How new, longer-life chips can help stretch your budget
Supported content When the inevitable upgrade arrives, you need future-proof silicon inside your data center hardware
-
Workload-optimized 97X4 and 9004 EPYC processors showcased by AMD
supported editorial New CPUs “push the boundaries” of what is possible in the data center performance, chip giant says
-
Minimising digital risk with cyber resilience
Whitepaper Building an intrinsically secure enterprise architecture