How the metaverse is powering next-gen digital twins
The metaverse will find a home in industrial settings by vastly expanding the benefits of simulation
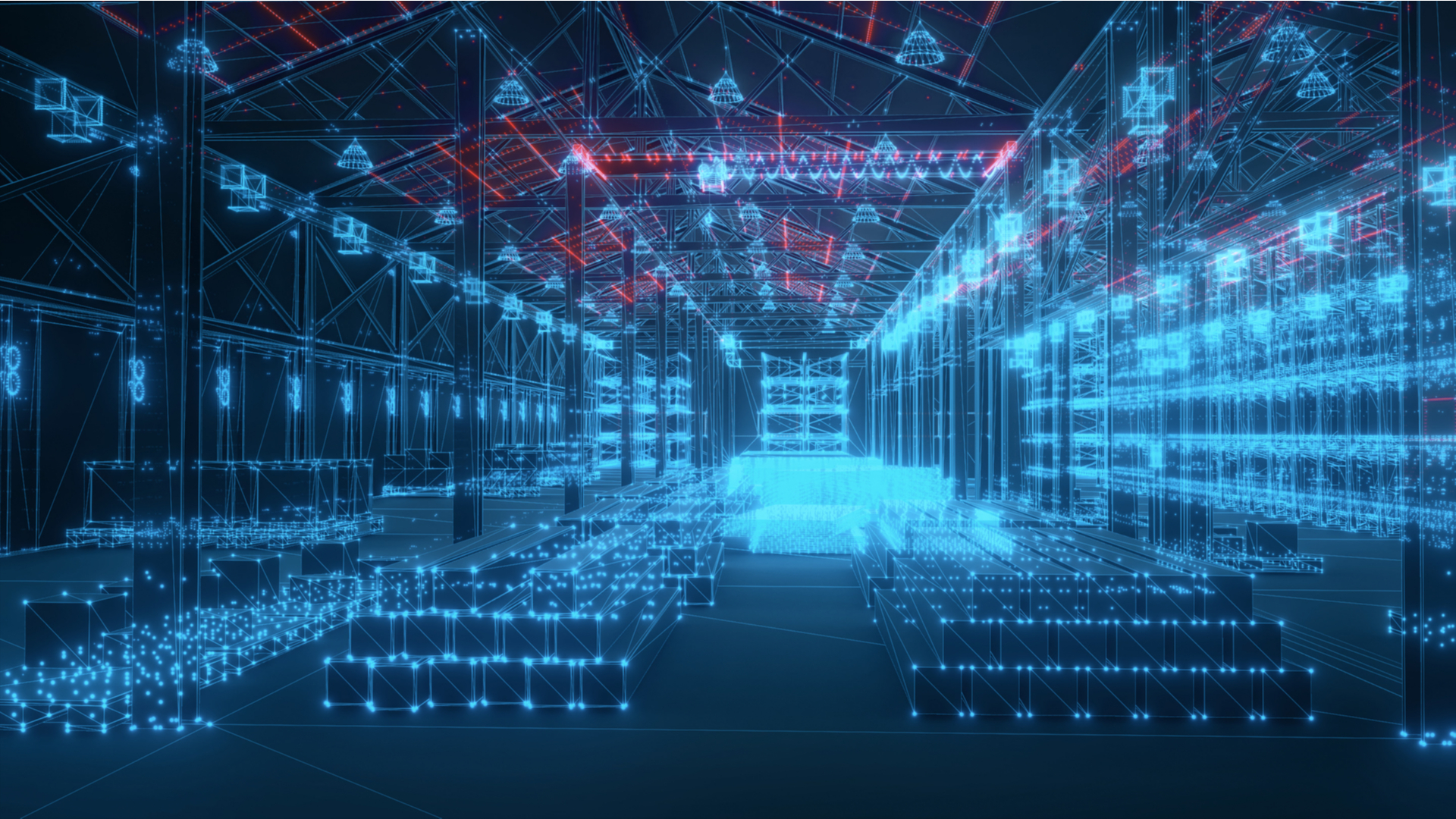
The industrial metaverse looks set to help transform almost any complex task that requires advanced modelling or 'next-phase' simulation tooling, moving it into pole position for solving multiple industrial and IT challenges.
According to Prith Banerjee, chief technology officer at Ansys, the metaverse will facilitate the modelling of laws of physics in greater detail than today's digital twins. Digital twins have been a great business asset for years, but already many ventures are pivoting to using the metaverse, as exemplified by the recent partnership struck between Siemens and Nvidia.
"If you have to change the design of a clay model of an aircraft wing for another run, each time you do it, it costs $10 million. Already, with a virtual wind tunnel, if we say a wing is going to fly, it’s going to fly," says Banerjee.
Banerjee defines digital twinning as modelling physical assets with sensor-enabled links between the physical asset and the virtual model – increasing accuracy, predictability, cost savings, and safety by further enabling remote working and accelerating innovation.
Finding a business case for the metaverse
Digital twin data can reveal how, say, a robot is performing today and what happens if different data is fed in on changing conditions, such as hotter weather or component failure. If bidirectional flows of information are enabled, automation working off digital twin data can do things like shut off heavy equipment in specified circumstances.
But metaverse takes the concept further still. "With internet powered by 3D, the metaverse is about making things as if you're almost actually there at the time," Banerjee continues. "With Zoom, I can see and hear you, but that's all. Metaverse is about how close can you go to absolute reality."
It can do modelling and predict consumer behaviour en masse, but engineering companies like Ansys seek 3D visualisations in real-time for fostering efficient, sustainable industrial design and manufacturing processes.
Sign up today and you will receive a free copy of our Future Focus 2025 report - the leading guidance on AI, cybersecurity and other IT challenges as per 700+ senior executives
"Companies building industrial systems, whether wind turbines or solar power plants, in the past, would have to physically go inside the lab with multiple R&D people working together. With the metaverse, the physics you once had only 'on the other end' become replicable everywhere," Banerjee explains.
RELATED RESOURCE
"If you compare gaming engines like Unity, they might have you driving around in a race car, it feels almost like reality, but not at the level of physics."
Mimi Keshani, co-founder and COO at Hadean, agrees, adding that gaming environments like CCP Games' Eve Online, with its multiple interacting entities, are created using "exactly the same tech" used to develop a synthetic training environment or digital twins of an existing process.
"You can save PhDs from repeating the same tiny difference in experiments over and over, those two minutes assigned to that eight hours of set-up to repeat exactly the same experiment," she points out. "Reduce complexity, reduce costs, reduce your footprint, make better decisions. Actually, simulation is our only power for telling the future."
Modelling to save money and innovate
Simulation is a highly complex emergent – dynamically evolving and learning in real-time – that’s being used to make decisions. These include data on hardware lifecycles, pan-national collaborative supply chains, sustainable manufacturing, or human behaviour en masse, Keshani agrees.
Of course, some of this is being done already for testing, evaluation and analysis of materials used, supply chains and more. The metaverse is about evolving towards still more accurate simulations, pending investment in remaining challenges around data quality and structuring, skills, security and interoperability. Also, abstractions must be built on top to achieve service-type technology set.
"(Companies should) use the standards and comply with things in ways that make sense across the industry," Keshani recommends, adding vendors are going to have to meet businesses halfway, offering more help beyond SDKs and recommending C++ training. "That's going to be a key challenge."
Tom Fairbairn, distinguished engineer at data mesh company Solace, notes its customer Unilever's 2000 ships transport cargo worldwide subject to ever-changing conditions rippling across its network. Millions of pounds can be lost or saved based on just-in-time decision-making, affecting not just Unilever but the whole supply chain. Even containers that are sitting empty cost money, Fairbairn says.
"They have satellite data tracking of ships. It's about grabbing that data as it occurs and doing something with it – juggling production schedules, updating logistics partners so lorries aren't sitting waiting for containers and so on," he says. "[They need a] virtualisation control tower, with a real-time view of exactly what's going on over the ocean."
Advanced machine learning can better triage inefficiencies and delays and help model knock-on effects related to specific decisions as they progress. When that can happen in real-time in both directions, that begins to indicate how the metaverse can deliver fuller visibility and control.
"You can determine and act on the variance in the outcomes, or potential outcomes, modelling effects of uncertainty," Fairbairn says.
Tapping into data to boost productivity
For Sylwia Kechiche, principal analyst, enterprise at network intel provider Ookla, applying AI and machine learning to large datasets merged with third-party sources in the metaverse will increase productivity and revenues across manufacturing.
"Data has become key," Kechiche confirms. "More intelligent planning tools can offer greater insights into sustainability, mapping out the entire product lifecycle."
Digital twins can be seen as early-stage – or a component of the metaverse – although standards for every aspect of the metaverse still require definition by the Metaverse Standards Forum (MSF) and others, including around real/virtual world integration, 3D asset interoperability, digital asset management, capabilities, avatars, privacy and more.
"2023 will see some more foundational work taking place," she adds, with the industry already picking off lower-hanging fruit, such as 3D mesh components for Microsoft Teams, AR/VR training and digital twin per se.
"In 2023, we could see more of a geo-digital twin – a fusion of geography and technology."
Certain technical requirements for latency and uploading will only arrive with 5G-Advanced from 3GPP Release 18 – although that standard is set to be frozen by the end of 2023, Kechiche adds.
Soubhagya Mohakud, vice president, Europe sales at Persistent Systems, confirms it's working on metaverse for educational demos, teaching simulations, and field ops support for remote servicing, maintenance and repairs. "This'll go a long way in improving 'first-time' fix rates and reducing costs."
Yet Jonny Stephens, consultant at Bearing Point, warns the lowest-hanging applications so far appear "squarely on the 'human' side" even though immersive screens and demos can certainly deliver business benefits.
"The metaverse can get dragged into discussions of extended VR. For modelling, quantum [computing] might be the tech to look at, rather than extended reality (XR)," he says. "For a lot of that, I don't really like the word 'metaverse'."
However described, advanced modelling and simulation that improves reporting on middleware and legacy applications running big complicated bits of machinery can save costs as well as maximise human abilities to interact with some systems, he agrees.
Fleur Doidge is a journalist with more than twenty years of experience, mainly writing features and news for B2B technology or business magazines and websites. She writes on a shifting assortment of topics, including the IT reseller channel, manufacturing, datacentre, cloud computing and communications. You can follow Fleur on Twitter.
-
AI tools are a game changer for enterprise productivity, but reliability issues are causing major headaches – ‘everyone’s using AI, but very few know how to keep it from falling over’
News Enterprises are flocking to AI tools, but very few lack the appropriate infrastructure to drive adoption at scale
-
Pegasystems teams up with AWS to supercharge IT modernization
News The duo aim to create deeper ties between the Blueprint, Bedrock, and Transform services
-
Untethered: How CIOs and CISOs are paving the way for the new hybrid workforce
Whitepaper Effective techniques to transition from exposed legacy infrastructure to an effective zero trust strategy
-
Creating successful supply chain planning transformations in the consumer industry
Whitepaper Think differently about SCP transformations and, in doing so, move into a better future for supply chains
-
Healthcare’s next chapter
whitepaper Revolutionizing how you care with EPR experts you can trust
-
Better together
Whitepaper Achieve more with Windows 11 and Surface
-
Transforming the enterprise
Whitepaper With Intel and CDW
-
Strategic app modernization drives digital transformation
Whitepaper Modernize your applications to address business needs both now and in the future